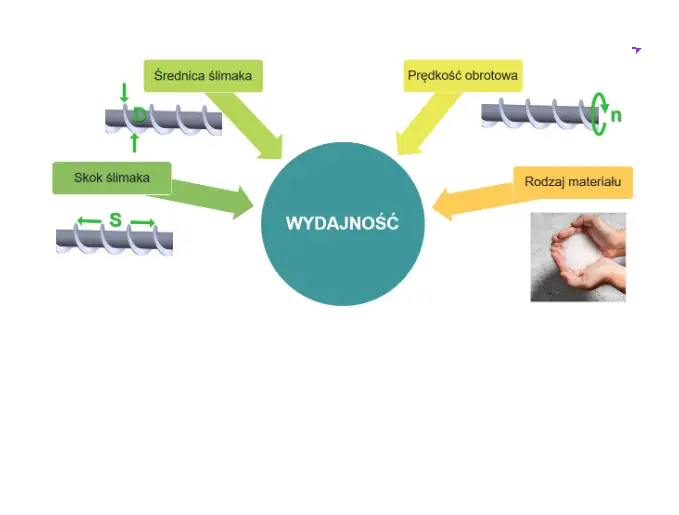
Jak przenośnik ślimakowy transportuje materiał ziarnisty?
W dużym skrócie odbywa się to w ten sposób, że spiralnie ukształtowane pióra ślimaka osadzone na obracającym się wale przesuwają materiał znajdujący się wewnątrz koryta. Jakie czynniki zatem wpływają na wydajność przenośnika? Po pierwsze, im większa średnica koryta, tym większa ilość materiału sypkiego znajduje się wewnątrz koryta, po drugie im większa prędkość obrotowa wału, tym większa prędkość przemieszczania materiału w korycie i po trzecie im większy skok (czasem zwany podziałką) pomiędzy kolejnymi piórami ślimaka, również tym większą prędkość przemieszczania materiału. Podsumowując, wydajność przenośnika ślimakowego zależy od średnicy zewnętrznej ślimaka, jego skoku i zadanej prędkości obrotowej.
Ale co z własnościami materiału sypkiego? Czy ten sam przenośnik będzie miał tę samą wydajność, gdy będzie transportował materiał lekki oraz ciężki? Otóż nie. Z pewnością znana jest zagadka: “co jest cięższe – kilo pierza czy kilo gwoździ?”. Pytanie bardzo podchwytliwe, ale odpowiedź jest logicznie prosta – ważą tyle samo! Ale co w przypadku, gdy sformułujemy ten problem inaczej, to znaczy “co waży więcej - metr sześcienny pierza czy metr sześcienny gwoździ”? Wyobraźmy sobie dwa identyczne pojemniki, oba wypełnione po brzegi – jeden gwoździami, drugi pierzem. Z pewnością znacznie cięższy będzie ten wypełniony gwoździami. Wynika to z faktu, że jeden gwóźdź waży znacznie więcej niż jedno pióro, zatem cały pojemnik również musi ważyć więcej.
Podobnie jest z materiałami sypkimi – pojedyncze drobinki materiału mogą mieć różną masę, np. grudka keramzytu jest znacznie lżejsza od podobnej grudki tłucznia. Dlatego w mechanice materiałów sypkich funkcjonuje pojęcie gęstość nasypowa, zdefiniowana jako masa jednego metra sześciennego materiału (kg/m3 lub t/m3). Ale gęstość nasypowa nie tylko zależy od masy pojedynczych drobinek czy brył. Zależy również od ich kształtu a dokładniej od tego czy nasze bryły będą gęsto upakowane w tym pojemniku czy też będzie sporo pustych przestrzeni pomiędzy nimi. Łatwo sobie wyobrazić, że dla materiałów o dużych przestrzeniach między bryłami gęstość nasypowa będzie mniejsza (po prostu będzie mniej materiału w danej objętości). Stąd o wydajności przenośnika ślimakowego decydować będzie też gęstość nasypowa materiału transportowanego.
Parametry konstrukcyjne przenośnika wpływające na jego wydajność
Wydajność jest w rzeczy samej najistotniejszym parametrem każdego urządzenia transportowego. Jednak aby zapewnić wymagany poziom wydajności, należy zapewnić odpowiednią moc napędu. Stąd, drugim istotnym parametrem eksploatacyjnym jest zapotrzebowanie na moc. Jednostka napędowa musi mieć odpowiedni zapas mocy, aby zapewnić wymaganą wydajność materiału. Zdanie to sugeruje, że moc potrzebna do przetransportowania materiału zależy od wydajności przenośnika. I jest to słuszne stwierdzenie. Im więcej i szybciej chcemy przetransportować materiały, tym więcej energii musimy dostarczyć do naszego układu. Ale pojawiają się również dodatkowe czynniki wpływające na wzrost zapotrzebowania na moc – są to opory ruchu występujące w czasie pracy przenośnika.
Źródła oporów ruchu są różne. Wynikają one z tarcia materiału o powierzchnię koryta, oporów obracania się wału w węzłach łożyskowych oraz uszczelnieniach, klinowania cząstek materiału znajdującego pomiędzy zewnętrzną krawędzią pióra a powierzchnią koryta, oporów przemieszczania materiału w korycie (wynikające z tarcia wewnętrznego występującego pomiędzy cząstkami materiału sypkiego) czy też opory związane z transportem materiału na pewną wysokość w przypadku przenośników ukośnych.
W obliczeniach mocy jednostki napędowej wszystkie te czynniki są ujęte w postaci jednego umownego współczynnika oporów ruchu charakterystycznego dla konkretnego materiału sypkiego. W literaturze można znaleźć obszerne tabele, w których zdefiniowane są współczynniki oporów ruchu dla poszczególnych materiałów sypkich. Obliczenie zapotrzebowania na moc napędu wynikające z uwzględnienia wydajności, oporów przemieszczania materiału, transportu na określoną wysokość mają jedynie orientacyjny charakter. Analitycznie trudno ocenić, jak zmieniają się opory ruchu (a w konsekwencji zapotrzebowanie na moc) w zależności od stopnia napełnienia koryta przez materiał sypki lub w zależności od ilości materiału znajdującego się w koszu zasypowym czy też opory związane z rozruchem przenośnika wypełnionego materiałem. Jedynym rozwiązaniem wydaje się przewymiarowanie napędu o pewien współczynnik bezpieczeństwa. Jednak są pewne rozwiązania, które pozwalają na uwzględnienie tych czynników. Są one związane z zastosowaniem zaawansowanych symulacji i komputerowych pozwalających na realistyczne odwzorowanie zachowania materiałów sypkich oraz ich interakcję z otoczeniem - maszyną lub urządzeniem. Ale ten temat zostanie szerzej rozwinięty w dalszej części artykułu, a także w serii kolejnych postów.
Jak dobrać parametry konstrukcyjne przenośnika?
Jak w takim razie dokonać obliczania pióra ślimaka, skoku linii śrubowej i prędkości obrotowej? W FMK intensywnie zajmujemy się tematyką projektowania przenośników w aspekcie ich optymalizacji. Nasze badania wykazały, że wzrost średnicy zewnętrznej, jak i wzrost długości skoku linii śrubowej ślimaka skutkują wzrostem masowej wydajności podajnika ślimakowego. Z kolei zapotrzebowanie na moc napędu spada ze wzrostem średnicy zewnętrznej oraz wzrostem długości skoku linii śrubowej ślimaka. Zaobserwowano, że tę samą wydajność transportową można zrealizować przy udziale różnych wariantów konstrukcyjnych przenośnika, przy czym moc potrzebna do przetransportowania materiału sypkiego nie jest jednakowa dla poszczególnych wariantów. Obserwacje te przekładają się wprost na oszczędności związane z energochłonnością urządzenia.
Jaką dobrać prędkość obrotową wału ślimaka? Kwestię tą należy rozpatrywać pod kątem kilku czynników: wydajności, zapotrzebowania na moc oraz rodzaju transportowanego materiału. Generalnie powszechnie przyjętą praktyką jest zmniejszanie prędkości obrotowej ze wzrostem gęstości nasypowej materiału. Innym czynnikiem jest abrazyjność materiału (jak silnie ścierny jest materiał). W przypadku materiałów o silnie ściernych własnościach prędkość obrotową wału należy zmniejszyć, aby zredukować efekt zużycia ściernego powierzchni piór ślimaka.
Symulacja transportu materiału w przenośniku dwuwałowym
Ale co w przypadku gdy mamy do zaprojektowania podajnik ślimakowy, który będzie wybierał materiał ze zbiornika, będzie to przenośnika dwu- lub więcej wałowy lub będzie to przenośnik rewersyjny? Jak już wspomniano wcześniej w takich przypadkach przychodzą z pomocą symulacje komputerowe pozwalające na realistyczne odwzorowanie zachowania materiałów sypkich.
Symulacje komputerowe w mechanice materiałów sypkich
Obecnie, w procesie projektowania nowych maszyn i urządzeń, coraz częściej wykorzystuje się komputerowe narzędzia wspomagania prac inżynierskich (ang. CAE Computer Aided Engineering). Duże moce obliczeniowe stacji roboczych oraz dostępność zaawansowanych programów i metod komputerowych pozwalają na wirtualne prototypowanie i symulowanie rzeczywistych zjawisk z bardzo dużą dokładnością, co jeszcze do niedawna nie było możliwe do odtworzenia przy pomocy metod numerycznych.
Zarówno analityczne, jak i komputerowe podejście do projektowania maszyn i urządzeń wymaga utworzenia modelu fizycznego badanego obiektu, a następnie opisania go za pomocą równań matematycznych. W klasycznym ujęciu modelowania model fizyczny stanowi pewną idealizacją rzeczywistego obiektu, a model matematyczny – jego formalny opis. Większość analitycznych metod projektowania maszyn i urządzeń opiera się na uproszczonych modelach fizycznych i matematycznych. Wyższy poziom złożoności modelu fizycznego wymaga użycia zaawansowanego opisu matematycznego, co z kolei jest kłopotliwe do zastosowania w praktyce inżynierskiej. W modelach komputerowych modele fizyczne są dużo bardziej złożone, dlatego odwzorowanie rzeczywistego obiektu lub zjawiska fizycznego jest dokładniejsze.
W przypadku symulacji zachowania materiałów sypkich powszechnie używa się Metody Elementów Dyskretnych (ang. DEM – Discrete Element Method). O samej metodzie i jej możliwościach w projektowaniu maszyn i urządzeń transportowych, przeróbczych oraz składujących poświęcony będzie osobny post. W przypadku projektowania przenośników ślimakowych metoda DEM daje ogromne możliwości. Dzięki symulacjom komputerowym jesteśmy w stanie dobrać najlepszy wariant konstrukcyjny przenośnika dla danego materiału sypkiego oraz przeznaczenia. Analizy komputerowe dają nam możliwość realistycznego zwizualizowania zachowania materiału w trakcie transportu, weryfikację stopnia napełnienia koryta przez materiał, obliczenie realnej wydajności przenośnika ślimakowego i danych technicznych oraz dobór właściwej jednostki napędowej, sprawdzenie stopnia zużycia ściernego piór czy optymalizację koszy zasypowych oraz sposobu podawania materiału do koryta.
Optymalizacja kształtu koszy zasypowych pod kątem energochłonności
Wszystkie te aspekty w żaden inny sposób nie są w stanie być ujęte przy projektowaniu przenośników. Budowanie prototypów i ich badanie jest nierealne ze względu na koszty i czas. Metody analityczne są zbyt uproszczone. Dlatego połączenie naszego doświadczenia konstruktorskiego, wieloletniej wiedzy z zakresu eksploatacji przenośników w różnych zakładach przemysłowych oraz umiejętności związanych z wykonywaniem symulacji komputerowych sprawia, że jesteśmy w stanie zaoferować przenośniki ślimakowe, które nie tylko przetransportują dany materiał z wymaganą wydajnością, ale wykonają to w ekonomiczny sposób, do tego będą odznaczały się oszczędnością materiałów konstrukcyjnych oraz większą trwałością na zużycie ścierne. Jako producent przenośników gwarantujemy Ci także profesjonalne doradztwo.